За время глобального финансового кризиса компания «Интерскол» получила доступ к самым современным западным технологиям, освоила производство сложной профессиональной техники и заняла рыночную нишу, которую из-за падения спроса освободили именитые конкуренты.
Компания «Интерскол», ведущий российский производитель электроинструмента, в сентябре прошлого года купила итальянскую фирму Felisatti, мирового лидера в области профессионального инструмента для обработки дерева. В результате этой сделки россияне получили парк новейшего производственного оборудования, включая единственный в своем роде роботизированный обрабатывающий комплекс, конструкторскую документацию на новые модели деревообрабатывающих машин и патенты на их ключевые узлы.
Покупка Felisatti положила начало большому проекту, который вывел наших инструментальщиков на мировой рынок хайтека — в сегмент профессионального электроинструмента. Сейчас интерсколовцы готовятся внедрить радикальную инновацию, которая обеспечит их технике качественное преимущество перед конкурентами.
Этот проект — своего рода мастер-класс «правильной модернизации», которая дает возможность не просто поменять одно «железо» на другое, а встать вровень с ведущими мировыми игроками — так, чтобы уже на следующем шаге опередить их. «Интерскол» показал, какие именно технологии стоит заимствовать за рубежом и как сочетать заимствованные технологии с отечественными инновациями, чтобы войти в число лидеров мирового хайтека.
Взять готовое
С момента своего основания «Интерскол» работал в сегменте электроинструмента бытового назначения (на рынке России и СНГ, где представлено свыше 120 марок, доля компании составляет 18%). Сегмент профессионального инструмента, где позиционируется техника с большой добавленной стоимостью, аккумулирующая в себе высокие технологии, был надежно занят элитными мировыми брендами — Bosch, Hitachi, Makita, DeWalt и проч.
Подвинуть грандов помог финансовый кризис. Из-за высокой цены продажи западных брендов сократились на 50–60%, и в профессиональном сегменте открылась ниша для относительно недорогого электроинструмента. Интерсколовцы увидели в этом свой шанс, но в их линейке профессиональной техники не было. Тогда они решили взять готовое — купить бизнес с состоявшимся продуктом и сформированным рынком. Но не любой бизнес, а обязательно нишевого лидера. Выбор пал на итальянскую фирму Felisatti, признанного технологического лидера в области электроинструмента для деревообработки. До кризиса торцовочные пилы, плоскошлифовальные машины и бороздоделы этой марки занимали около 15% рынка в Европе и почти 80% в Израиле и странах Северной Африки.
Сто процентов акций Felisatti, активы которой оценивались в 20–25 млн евро, интерсколовцы приобрели за 2,7 млн евро. По условиям сделки все перешедшее к россиянам производственное оборудование нужно было оперативно вывезти с занимаемых площадей. Вопрос: куда? По всем расчетам выходило, что перевозить его следовало в Китай — на завод корпорации Crown, партнера «Интерскола» по совместному предприятию Interskol Crown Group (см. «Оседлать дракона» в «Эксперте» № 28 за 2009 год). В Китае имеются все условия для успешного развития нового бизнеса: кооперация производителей комплектующих налажена, трудовые ресурсы в избытке, а чиновничий произвол и бюрократические препоны сведены к минимуму. Однако в «Интерсколе» приняли решение в пользу России.
«Я понял, что, если мы перевезем все это в Китай, мы здесь, в России, никогда не освоим передовые западные технологии, не научимся работать на сложном современном оборудовании», — этот довод стал решающим для Сергея Назарова, председателя совета директоров компании. Высокотехнологичное «железо» отправилось из Италии на Быковский электроинструментальный завод (БЭЗ) — российскую производственную площадку «Интерскола». Но добралось оно туда нескоро.
На российской таможне груз задержали под предлогом неправильно оформленной документации и продержали на складе временного хранения три с лишним месяца. За это время его там изрядно раскурочили. Так, два высокопроизводительных сборочных конвейера интерсколовцы получили назад в виде груды искореженного металла. При этом за ввоз суперсовременного высокотехнологичного оборудования, аналогов которого в России нет и в обозримом будущем вряд ли будет, компания заплатила в общей сложности более 700 тыс. долларов. «Мы пригнали из Италии 56 фур с оборудованием — больше тысячи тонн, — говорит Сергей Назаров. — Все вместе с доставкой, растаможкой, ремонтом и монтажом нам обошлось в пять миллионов евро»
Хайтек по китайской себестоимости
Самое ценное приобретение «Интерскола» — пятикоординатный обрабатывающий комплекс. Это эксклюзив, каких даже в Европе единицы. С виду агрегат напоминает многомодульную космическую станцию. В просторном зале цеха он возвышается почти до потолка, а по площади занимает столько же, сколько небольшой коттедж. Внутри «станции» организована своего рода карусель: по кругу движутся и вращаются вокруг своей оси восемь платформ с каркасами, по-западному — палет. На палетах с помощью особых зажимов крепятся обрабатываемые детали, от 16 до 32 штук на одной палете.
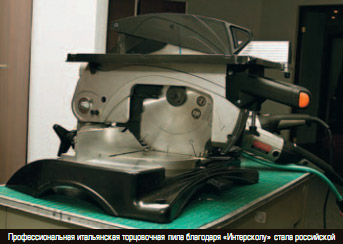
Все, что происходит с деталями в недрах «станции», скрыто от глаз за глухими металлическими стенами. Заглянуть внутрь удается только через решетчатое окошко в боковом модуле. Там находится склад инструмента: на узких стеллажах разложены резцы, сверла, фрезерные головки, развертки — всего 256 наименований инструмента, каждый в своем гнезде. Время от времени над стеллажами складского отсека зависает главная рабочая рука-манипулятор. Тогда оживает складской манипулятор: двигаясь строго по вертикали и горизонтали, он забирает у «руки» инструмент, который ей больше не нужен, аккуратно кладет его в соответствующее гнездо, быстро находит другой и вставляет в специальный захват «руки». «Рука» возвращается к «карусели» с палетами выполнять очередную операцию: сверлить, шлифовать, растачивать или нарезать резьбу.
Этого промышленного робота стоимостью 1,2 млн евро специально для Felisatti изготовила итальянская фирма МСМ, мировой лидер в области автоматизированных обрабатывающих центров. Ей удалось собрать в одном агрегате несколько обрабатывающих центров с разными функциями и сделать этого робота полностью самостоятельным. Человек ему нужен только для того, чтобы принять готовые детали и загрузить новые.
На БЭЗе итальянский комплекс заенил собой целый цех — больше двух есятков обычных токарных, фрезерных сверлильных станков, отставших от тальянского робота на несколько покоений. «Мы не просто поменяли старое борудование на более современное. Мы зменили саму концепцию производства, — подчеркивает Владимир Иванов, гееральный директор БЭЗа. — Раньше мы а своих станках работали по принциу “один человек — один станок — одна перация”. В итальянском комплексе реализован другой принцип: “один человек — один станок — все необходимые операции”».
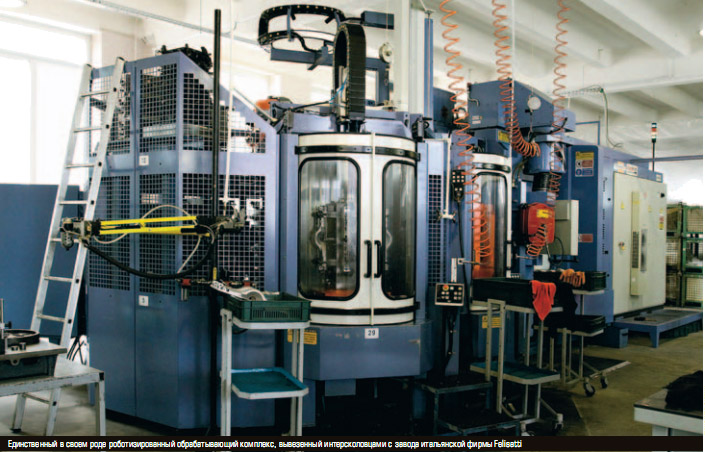
Подобные роботизированные комплексы — шедевры западного станкостроения. Обычное же оснащение хорошего европейского завода — полностью автоматизированные обрабатывающие центры. Создание такого класса оборудования стало ответом развитых стран на два главных вызова 1990-х: вала дешевой китайской техники, хлынувшей на все рынки, и дефицита инженерных кадров, который остро ощутили даже ведущие технологические державы вроде Германии.
Производительность такого центра минимум в пять раз выше, чем у обычных станков. Точность обработки выше на порядок. А брака правильно налаженное автоматизированное оборудование не выдает вовсе (в Китае до недавнего времени 20% брака считалось нормой). Все это вместе позволяет европейцам выпускать высокотехнологичный продукт с себестоимостью, близкой к себестоимости китайского ширпотреба, а значит, оставаться конкурентоспособными в условиях агрессивной экспансии Китая. «Добиться на европейском заводе китайской себестоимости — серьезное достижение, — подчеркивает Сергей Окунев, заместитель генерального директора “Интерскола”. — При этом по уровню качества и потребительским свойствам европейская техника отличается от китайской, как “Мерседес” от “Запорожца”».
Без подобного оборудования, уверен Сергей Назаров, наладить в России массовый выпуск конкурентоспособных высокотехнологичных продуктов практически нереально. «Европейцы ушли от нас на много лет вперед. Мы должны завозить их высокопроизводительное оборудование, их технологии в Россию. Таким образом мы достаточно быстро поднимем технологический уровень многих отраслей нашей промышленности, — утверждает Назаров. — Тем более что сегодня все это можно взять в Европе почти за бесценок»
Транснациональный инструментальщик
Компания «Интерскол», ведущий российский разработчик и производитель электроинструмента, — преемник советской инженерной школы электроинструмента. Она была создана в 1991 году на базе Всесоюзного НИИ механизированного и ручного строительно-монтажного инструмента (ВНИИСМИ). В состав компании входит научно-инженерный центр, ведущие специалисты которого выходцы из ВНИИСМИ.
В 2008 году интерсколовцы создали совместное предприятие с корпорацией Crown Power-Tool Manufacturing, крупнейшим китайским производителем электроинструмента. СП получило название Interskol Crown Group (ICG), доля российской компании в нем 50%. Таким образом, российские инструментальщики получили в свое распоряжение китайскую производственную базу и китайскую рабочую силу, а также контроль над стремительно набирающим силу конкурентом.
До 2009 года компания работала только в сегменте электроинструмента бытового назначения. При этом перфораторы, дрели, шуруповерты, шлифовальные машины и другой инструмент под маркой «Интерскол» ни по техническим параметрам, ни по надежности не уступали аналогам ведущих мировых игроков, позиционированным в сегменте профессиональной техники. Оборот компании составлял 140 млн долларов, она занимала 18% рынка России и СНГ.
В 2009–2010 годах «Интерскол» купил две европейские фирмы — итальянскую Felisatti (100%) и испанскую Casals (51%) — и стал глобальным игроком с оборотом 170 млн долларов.
Прорыв в профессионалы
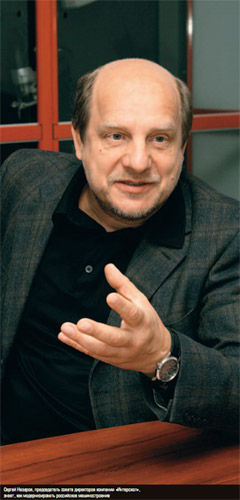
На освоение заимствованных на Западе технологий интерсколовцы потратили год — отремонтировали раскуроченные на таможне конвейеры, научились у итальянских специалистов делать сложные настройки в бортовом компьютере роботизированного комплекса и выстроили кооперацию.
Самым трудным оказалось найти в России поставщиков заготовок и комплектующих. Пока «Интерскол» договорился только с одной небольшой фирмой «Литформ» из Калуги, у нее инструментальщики будут покупать литые алюминиевые заготовки. А все комплектующие, включая винтики, шайбы, пружинки, гайки-барашки и даже резиновые уплотнительные кольца, оказалось выгоднее приобретать в Европе: они обходятся в три-четыре раза дешевле российских аналогов, а по качеству превосходят их на порядок. «Сегодня кооперации для производства серьезного профессионального инструмента в России нет» — к такому выводу пришли интерсколовцы, перебрав десятки потенциальных поставщиков. Это означает, что перевооружение отдельных, даже сравнительно крупных компаний не сможет поднять общий технологический уровень российской промышленности. Необходима не индивидуальная, а массовая модернизация, охватывающая все обрабатывающие секторы.
Дебют «Интерскола» на мировом рынке хайтека состоялся в марте этого года. К настоящему моменту на европейском рынке продана уже тысяча сделанных в России профессиональных пил и шлифовальных машин. «Впервые за всю историю нашей страны мы начали экспортировать электроинструмент в Западную Европу — во Францию, в Италию, Грецию, — подчеркивает Сергей Назаров. — Такого не было ни в эпоху СССР, ни в постсоветское время». К 2012 году объем экспорта интерсколовской профессиональной техники должен достичь 40 тыс. штук, что эквивалентно 8 млн евро в год.
После успешного дебюта перед интерсколовцами встала задача закрепиться в профессиональном сегменте. Для этого они купили еще одного сильного нишевого игрока — испанскую фирму Casals (профессиональный электроинструмент для обработки дерева этой фирмы известен в мире под брендом Freud, по некоторым группам продуктов его рыночная доля доходила до 30%). Как и в случае с Felisatti, контрольный пакет акций Casals (51%) россияне получили с кризисным дисконтом. «Из продуктов Casals нам интересны в первую очередь профессиональные фрезерные и шлифовальные машины — они дополнят линейку деревообрабатывающего инструмента Felisatti, расширив наше предложение на рынке профессиональной техники», — говорит Сергей Окунев, ставший председателем совета директоров Interskol Power Tools Spain (так назвали новое юрлицо).
В результате сделки с Casals российские инструментальщики получили также производственную площадку в Европе. Ее достоинства — новейшее оборудование и близость к европейскому рынку, который интерсколовцы намерены осваивать в первую очередь.
Дешевле, чем у европейцев
На испанском заводе нет уникальных интегрированных комплексов, подобных «космической станции» МСМ, но есть 12 современных, полностью автоматизированных обрабатывающих центров. Работой такого автомата нельзя не залюбоваться. Манипулятор безошибочно выбирает из внушительного барабана нужную насадку, направляет обильную струю охлаждающей жидкости точно на ту грань детали, которую обрабатывает резец, ловко переворачивает деталь, меняет резец, снова точит, вырезает, шлифует и делает все это так быстро, четко и аккуратно, как гомо сапиенсам и не снилось. Рабочий подходит к центру-автомату лишь изредка, чтобы забрать готовые детали, которые рукаманипулятор аккуратно выкладывает на движущуюся ленту. Поэтому на испанском заводе так же пустынно в разгар рабочего дня, как на российском после окончания очередной смены.
На автоматизированных центрах Casals, которые в отличие от оборудования Felisatti не нужно было никуда перебазировать, наши инструментальщики быстро наладили выпуск собственных перфораторов — самого сложного и технически совершенного своего продукта. Их перенесли на завод Casals из Китая, где производство нескольких моделей интерсколовских перфораторов было организовано в 2008 году. Себестоимость «испанского» перфоратора оказалась не выше «китайского» при колоссальной разнице в качестве. Тем самым «Интерскол» доказал, что в Европе действительно реально производить хайтек по китайской себестоимости.
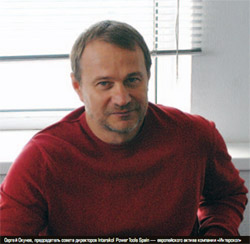
Но для того, чтобы занять открывшуюся в профессиональном сегменте нишу не очень дорогого инструмента, необходимо дополнительно снизить его себестоимость — теперь уже относительно Европы. Для этого наши инструментальщики намерены перевести отдельные технологические операции из Китая в Испанию, а из Испании — в Россию. Так, в Россию планируется перевести всю высокотехнологичную обработку. «Всю обработку мы будем вести в России, на роботизированном комплексе МСМ. Сегодня это дешевле, чем в Китае и в Европе, потому что там, где китайцам нужно поставить двадцать человек, а европейцам пять, у нас работает один человек — оператор комплекса МСМ, — объясняет Сергей Назаров. — Наш комплекс одновременно обрабатывает от 128 до 256 разных деталей. В Китае то же самое сделают на десяти-пятнадцати станках, в Европе — на пяти-семи станках. А когда ты переносишь деталь с одного станка на другой, теряется главное — точность. На нашем комплексе мы можем делать любые отверстия, расточки и заточки с микронными допусками. А углы наклона торцовочных пил выдерживать с точностью до трех-восьми минут, это лучше, чем у многих признанных лидеров рынка». За счет грамотного распределения функций между китайскими, европейскими и российскими активами интерсколовцы рассчитывают снизить себестоимость своего профессионального инструмента на 10–15%. То есть делать хайтек дешевле, чем у европейцев.
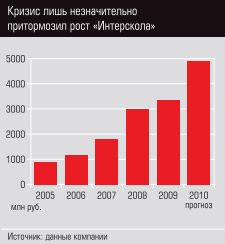
Таким образом, у «Интерскола» формируется широкая линейка сравнительно недорогого профессионального электроинструмента для обработки дерева. Помимо наиболее удачных моделей из ассортимента фирм Felisatti и Casals в нее войдут и несколько новых машин, разработку которых наши инструментальщики заказали лучшей итальянской инжиниринговой фирме Coledos. «У нас на проектирование простой пилы и подготовку ее к производству уходит до двух лет, а итальянцы сделают нам очень серьезную машину всего за шесть-семь месяцев, — отмечает Сергей Назаров преимущества специализированного инжиниринга. — Это будет новая модель торцовочной пилы с использованием уникального узла, патент на который принадлежал фирме Felisatti, а теперь принадлежит нам. Это шарнирное соединение, которое обеспечивает высокую точность обработки дерева. Таких машин не будет ни у кого».
Тем самым всего за год российская компания догнала мировых грандов, контролировавших сегмент профессиональной техники. Догнала и по ассортименту, и по техническим параметрам. Но останавливаться на этом наши инструментальщики не собираются. Они намерены занять в сфере профессиональной деревообработки лидирующие позиции. Для этого к тому, что куплено и разработано за рубежом, нужно добавить некую изюминку, которая не просто выделила бы интерсколовскую технику среди других брендов, а обеспечила бы качественные преимущества перед конкурентами.
Вентильная революция
Такие преимущества дают инновации, созданные сильными отечественными научно-инженерными школами. Для «Интерскола» инновацию-изюминку разработали специалисты Ижевского механического завода (ИМЗ) совместно с учеными Новосибирского госуниверситета. Эта команда сохранила свои компетенции со времен крупного технологического проекта 1980-х, когда ИМЗ было поручено создать высокоточные гироскопы для оборонки. Спустя три десятилетия эта школа по заказу интерсколовцев разработала вентильный двигатель (ВД) — альтернативу традиционным электродвигателям, которыми комплектуются все разновидности электроинструмента.
Основа вентильного двигателя — постоянные магниты. Они хороши тем, что в отличие от контактов электрической цепи обычного двигателя никогда не перегорают от перегрузок. Второе достоинство ВД — отсутствие редуктора и других изнашивающихся механических составляющих. Две эти особенности обеспечивают вентильному двигателю завидную живучесть. «Обычные двигатели, которые сейчас используются в электроинструменте, живут недолго, всего триста максимум пятьсот часов. По сравнению с ними вентильный двигатель будет практически вечным, его ресурс более десяти тысяч часов», — рассказывает Сергей Окунев.
Второе после долговечности достоинство ВД — экономичность. «Удельная мощность на грамм веса у вентильного двигателя в полтора раза больше, чем у обычного коллекторного. Это позволит экономить 15–20 процентов электроэнергии, — поясняет Сергей Назаров. — И КПД нового двигателя значительно выше: 70– 75 процентов против 55 у традиционного». Есть у ВД и третий немаловажный плюс — работает он абсолютно бесшумно. Вентильные двигатели давно используются, в частности, в стационарных промышленных станках. Однако все попытки создать их модификации для ручного инструмента до сих пор проваливались: продукт получался неконкурентоспособным. Так, ВД для торцовочной пилы, разработанный по заказу американской компании Black & Deсker, оказался дороже, чем целиком пила с традиционным электродвигателем. Российским инженерам, судя по всему, удалось сделать инновацию дешевой: по словам Сергея Назарова, цена ВД будет выше цены традиционного максимум на 10–15%. Чтобы интегрировать ВД в ручной инструмент, потребовалось не только минимизировать габариты и вес двигателя, но и создать для него «мозги» — электронную систему управления, которая сглаживала бы пиковые нагрузки при входе рабочего элемента в дерево, подбирала для каждой породы древесины оптимальное число оборотов и т. д. Сейчас уже можно говорить, что команда ижевских и новосибирских специалистов с этой задачей справилась. В настоящее время инженеры «Интерскола» проводят испытания опытных образцов вентильных двигателей. Выход инновации на рынок запланирован на 2011 год. В масштабах отрасли это будет настоящая революция. Новыми двигателями планируется комплектовать до 20% всего деревообрабатывающего инструмента «Интерскола». Первыми станут торцовочные пилы из линейки Felisatti, на них ВД установят сразу после завершения испытаний и отправят на экспорт. С таким инновационным продуктом «Интерскол» выйдет на первое место в мире по объемам продаж профессиональных торцовочных пил.
Автор статьи Ольга Рубан
источник - сайт выставки MITEX 2010
Оценка материала: | ![]() ![]() ![]() ![]() ![]() |
Средняя оценка: 0 | Всего голосов: 0 |